Screw jacks are used globally to lift, position, align and support loads. Their simple designs make them flexible enough for various uses.
Available varieties of screw jacks include worm gear, bevel gear and ball screw jacks; each offers their own advantages and drawbacks.
Lifting
There is a range of screw jacks on the market designed for specific tasks and applications, all offering exceptional strength. Available in various sizes and load capacities, they allow users to lift and lower a variety of loads with ease.
Jacks come in various designs; depending on your application they could feature either a travelling screw or lead screw that moves linearly up and down. Determining which jack best meets your needs depends on several factors including travel rate or speed, efficiency, accuracy, duty cycle cycle cycle duration and price.
Travel screw jacks tend to be more cost effective and accurate than ball screw jacks, as well as offering greater versatility by being capable of accommodating more duties cycles without overheating or damaging their screw.
Assembling
Screw jacks, commonly referred to as mechanical actuators, can be used to lift, position, align and support all sorts of loads. Their common configuration – usually using a worm gear system – converts motor or manual input energy into linear movement via rotational movement.
Screw Jacks come in various designs and capacities, making them suitable for applications requiring precise positioning with high degrees of control. They can be combined with motors to form drive systems, or can even be mounted individually.
Screw jacks are often the superior solution when lifting or supporting heavy loads, as they are more convenient and reliable than hydraulic rams in maintaining constant pressure while moving the load. Hydraulics require considerable energy consumption in maintaining constant pressure during their movement of a load.
Screw jacks are mechanical devices used for lifting heavy loads vertically or horizontally. There are various types of screw jacks, and each type is designed for specific applications. One such type is the travelling nut screw jack.
The travelling nut screw jack operates by having a nut that travels along the length of the screw shaft, which rotates to lift or lower the load. This type of screw jack is commonly used in applications where high efficiency and precision are required, such as in the positioning of heavy machinery or in the adjustment of large structures.
One advantage of the travelling nut screw jack is that it provides greater control over the lift and lowering of loads due to its precise positioning capabilities. Additionally, this type of screw jack can handle heavier loads compared to other types of screw jacks.
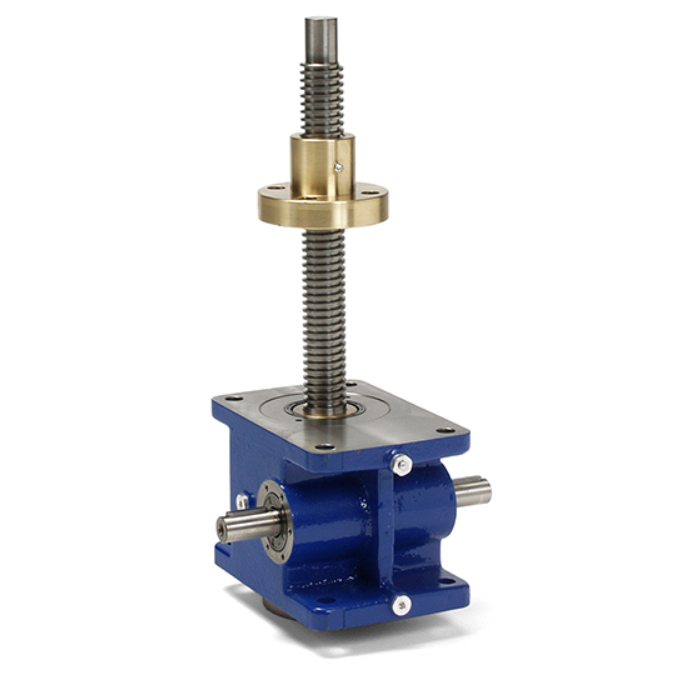
Overall, the travelling nut screw jack is a reliable, efficient, and precise lifting solution for many industrial applications.
Adjusting
Screw jacks are an indispensable way of lifting, lowering, pushing or pulling heavy loads with precision and efficiency. Furthermore, they play an integral part in automating machinery for safety or legislative reasons; especially those which automate loading and holding operations.
Screw jacks can be used to push, pull, tension, lock, unlock, tilt pivot roll slide lift or lower anything from several kilograms up to thousands of tonnes. Their electro-mechanical solution to linear motion uses less energy than hydraulic actuation systems.
There are three general types of screw jacks: machine/worm gear, ball screw and bevel gear. Their type depends on whether or not the lead screw translates, keyed or rotates/travels during operation.
Holding
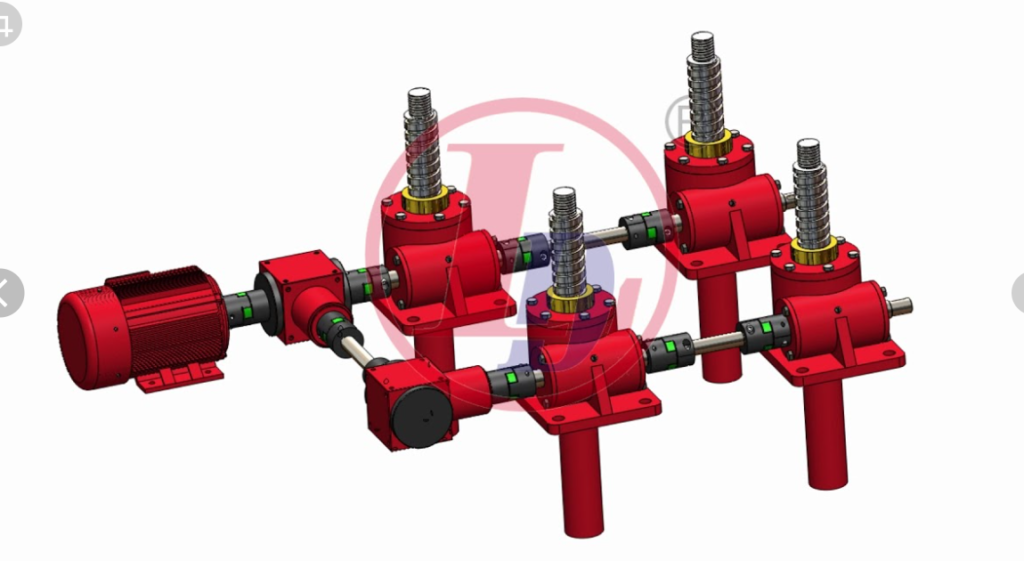
Screw jacks are industrial support mechanisms used for holding loads in various industrial applications. They may feature either an ACME (ACME or trapezoidal) thread or ball screw thread and can support loads up to 100 tons.
Designers should carefully consider travel length and load capacity when selecting a jack. Longer operating levers reduce mechanical advantage, increasing friction in screw threads and restricting their lifting capacities.
Modifying the design of a jack can accommodate heavier loads and quicker cycle times by altering its lift screw type, gear set or travel nut size. Designers must take into account column buckling when using lifting screws with compressed loads that may lead to loss of torque.
Anti-backlash control is another essential feature of a screw jack that helps avoid vibrations and premature wear on its mechanism when loads reversal occurs, especially when moving large loads which require precise synchronicity between movements.